In automotive manufacturing, the margins for error are extremely small, while the demands for precision and efficiency are exceedingly high. The components that go into our vehicles, from the smallest screws to the engine blocks, must adhere to strict safety standards, often requiring tight tolerances that leave little room for deviation. This level of precision ensures the safety of all automotive products and their reliability and performance over time.
At the heart of this intricate and demanding process are the tooling and machining strategies used. Carr Lane Mfg. specializes in providing the essential tooling components that empower automotive manufacturers to meet the exacting standards of the industry. Our solutions help manufacturers achieve the necessary precision and repeatability needed to succeed in automotive manufacturing, not only to maintain industry standards but also to push the boundaries of what’s possible in automotive engineering.
Selecting the proper tooling and leveraging the best machining strategies is essential to meeting the demanding standards and requirements of automotive manufacturing. In this article, we explore the expert strategies and advanced technologies that make high precision and efficiency possible. Whether you’re directly involved in automotive manufacturing or provide support to those who are, these tactics are essential in navigating the future of automotive part tooling and machining.
The Significance of Part Tooling & Machining Methods in the Automotive Industry
The quality of every component, no matter how small, significantly impacts the overall performance and safety of a vehicle. Tooling and machining are critical components in the production process, where precision and efficiency are not just goals but necessities. Commonly used tooling in this sector includes dies for stamping body parts, molds for plastic components, and precision jigs and fixtures to ensure the exact machining of various vehicle parts. Standard machining methods like milling, turning, and grinding are staples in manufacturing these components, with each method having specific benefits depending on the material and part requirements.
The tooling and machining methods chosen directly influence the manufacturing speed, cost-efficiency, and quality of the automotive parts produced. Efficient tooling reduces machine time and wear, lowers the cost per part, and minimizes downtime due to maintenance or failures. Effective machining, on the other hand, ensures that parts meet the strict tolerances required for assembly and function, contributing to the vehicle’s overall reliability and performance.
However, achieving this high level of precision and efficiency comes with many challenges. Material selection is one example where manufacturers must balance cost, machinability, and performance. For instance, aluminum may be chosen for its lightness and corrosion resistance but requires different tooling and machining strategies compared to more traditional steel parts. Precision requirements are another hurdle; automotive parts often require tolerances within thousandths of an inch to ensure proper fit and function. Lastly, production speed is crucial in a competitive market where the ability to rapidly produce large volumes of parts can be as important as the quality of the parts themselves.
Material Considerations for Automotive Part Manufacturing
The choice of materials in automotive manufacturing plays a pivotal role in determining the efficiency, sustainability, and performance of the final product. Three primary materials dominate the landscape: steel, aluminum, and composites. Each of these materials brings its own set of advantages and challenges, particularly when it comes to machining and tooling.
Steel has long been the backbone of automotive manufacturing due to its durability and cost-effectiveness. It is especially prevalent in producing structural components, where strength is paramount. However, machining steel requires robust tooling solutions that can handle its hardness and abrasiveness, which can significantly wear down cutting tools.
Aluminum is increasingly favored in the automotive industry for its lightweight and high-strength properties, which are crucial in enhancing fuel efficiency and reducing emissions. In fact, the use of aluminum in both electric and non-electric vehicles in North America is projected to see a 24% increase by 2030. While aluminum is easier to machine than steel due to its softer nature, its high malleability presents challenges such as rapid tool wear and difficulty controlling the machining process.
Composites, such as carbon fiber reinforced polymers, are used in high-performance and luxury vehicles to achieve further weight reduction and strength enhancement. These materials are notoriously complex to machine due to their abrasive nature and the risk of delamination or fraying during the machining process. Specialized tooling and machining strategies are required to effectively work with composites.
When selecting materials for automotive parts, several factors should be considered to ensure optimal performance and manufacturability:
- Application-Specific Requirements: Determine the mechanical and environmental stresses the part will face. For structural components, strength and durability are crucial, while for interiors, aesthetics might also be considered.
- Machinability: Assess how easily the material can be machined, including considerations for tool wear and the type of machining needed.
- Cost-Effectiveness: Consider both the raw material cost and the associated manufacturing costs, including tooling and machining time.
For instance, while aluminum might be preferable for reducing vehicle weight, it may not always be suitable for all parts due to its lower modulus of elasticity and strength compared to steel. Engineers must balance these material properties with the part’s functional requirements and the overall manufacturing costs.
Advanced Tooling Technologies Transforming Automotive Manufacturing
Once you’ve selected the ideal material, it’s time to determine the best tooling and machining methods to efficiently and precisely turn that material into a functional vehicle component. Luckily, there are many advanced tooling technologies that are revolutionizing the automotive industry and providing the precision and repeatability needed to enhance automotive manufacturing operations.
Multi-Tasking Machines
Multi-tasking machines integrate various machining operations, such as milling, turning, and drilling, into a single-machine setup. This integration not only streamlines the production process but also enhances precision and lowers overall production costs by reducing the need to move parts across multiple machines, minimizing errors, and increasing throughput. These machines are particularly beneficial for complex parts that require multiple machining processes, offering significant time and cost savings.
High-Speed Milling (HSM)
High-speed milling (HSM) machines mill a workpiece with high speeds and feed rates with specialized cutting tools. This method allows for the efficient machining of automotive parts with intricate details and fine finishes. HSM reduces the time it takes to machine parts, decreases heat generation, and minimizes tool wear, making it ideal for both hard and soft materials. The result is a smoother surface finish, which can reduce or eliminate the need for additional finishing processes.
Additive Manufacturing
Commonly known as 3D printing, additive manufacturing is revolutionizing automotive part production by allowing for the creation of complex components that would be challenging or impossible to make with traditional methods. This technology can create prototypes, custom tooling, and lightweight, structurally complex components directly from CAD data. The ability to layer materials precisely offers unparalleled design freedom, promoting innovation in automotive design and functionality while potentially reducing material waste and overall production costs.
Tool Condition Monitoring Systems
Tool condition monitoring systems are essential for maintaining high levels of quality and efficiency in automotive machining. These systems use sensors and advanced analytics to continuously assess the condition of cutting tools, providing real-time feedback that can prevent tool failure and unplanned downtime. By detecting wear and tear early, these systems allow for timely tool replacement and adjustment, ensuring consistent manufacturing precision and extending the lifespan of machining equipment.
Robotics and Automation
Robotics and automation systems can enhance both productivity and consistency across production lines, from automating tool changes to handling parts before and after machining. Robots are employed for tasks ranging from material handling and welding to assembly and painting, ensuring that operations are not only swift but also precise. Automated systems can operate around the clock and in environments that may be hazardous for human workers, further increasing production output and reducing the likelihood of errors or accidents.
Essential Machining Strategies for Maximum Efficiency
To stay competitive in the automotive manufacturing industry, efficiency in machining processes is not just a goal, but a necessity. Streamlining these processes while minimizing waste is crucial for maintaining profitability and sustainability. Maintaining and managing tools is also crucial for ensuring consistent performance and achieving high-quality results, including regular inspection, cleaning, and necessary tool replacement. Here are some best practices and specific techniques for setting up machining processes that maximize efficiency:
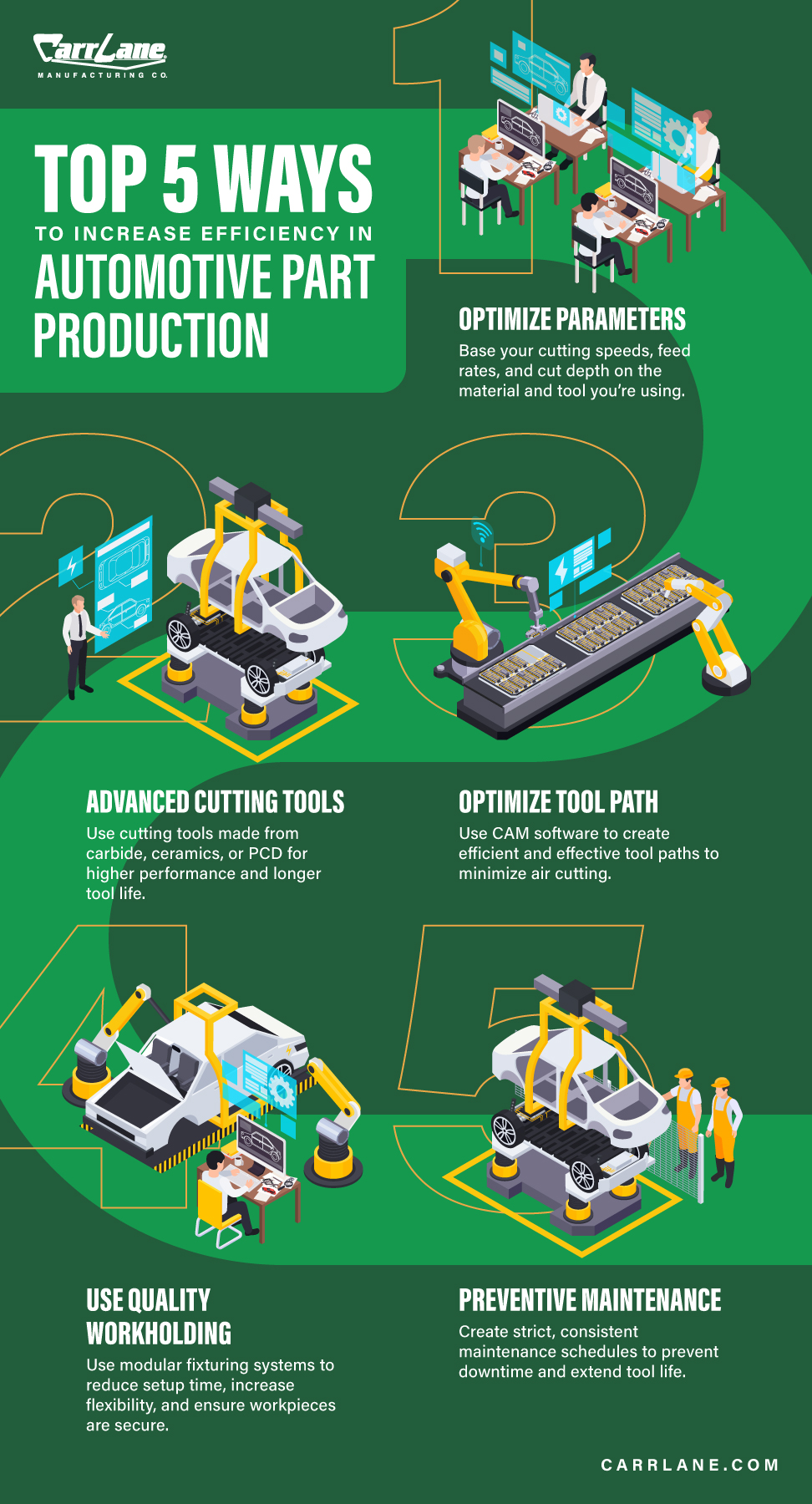
- Optimize Machining Parameters: Effective machining starts with optimizing cutting speeds, feed rates, and the depth of the cut. These parameters should be carefully tailored to each material and tooling combination used. Optimizing the cutting speed and feed rate can significantly enhance efficiency and extend tool life without compromising the quality of the part. Adjusting the depth of the cut optimizes the material removal rate, which is essential for maintaining the stability of the tool and the integrity of the machine.
- Use Advanced Cutting Tools: Using cutting tools made from advanced materials such as carbide, ceramics, or polycrystalline diamond (PCD) can achieve higher performance and longer tool life. Selecting tools with geometrics optimized for specific automotive applications can reduce machining force, improve chip evacuation, and enhance overall cutting efficiency. These high-performance tools are crucial to maintaining consistency and quality, especially in high-volume automotive production.
- Tool Path Optimization: Utilizing advanced Computer-Aided Manufacturing (CAM) software to create efficient and effective tool paths minimizes non-productive air cutting and ensures that the tool is engaged with the material as much as possible. This tactic can reduce cycle times and improve the overall throughput of machining operations.
- Advanced Fixturing & Workholding: Advanced fixturing solutions ensure that workpieces are securely held during the machining process and are easy to load and unload. Modular fixturing systems are particularly beneficial as they reduce setup time and increase flexibility, allowing for quick switches between different jobs. Carr Lane Mfg. offers a range of clamping solutions, fixture plates, and both standard and heavy modular fixturing systems to enhance machining efficiency and repeatability in a variety of automotive manufacturing applications.
- Preventive Maintenance: Maintaining a strict schedule for machine maintenance prevents unexpected downtime and ensures consistent performance. This includes regular checks and servicing as per the manufacturer’s guidelines. Additionally, integrating sensors and IoT technology can facilitate predictive maintenance, where data-driven insights predict potential failures before they occur, allowing for proactive repairs or adjustments.
Ensure Precision with Quality Control and Testing
Quality control is another cornerstone of automotive part production, where precision isn’t just about meeting specifications, but also about ensuring safety, reliability, and compliance with stringent industry standards. As vehicles become more sophisticated, the demand for precision in every component increases, making effective quality control measures more critical than ever.
To meet these high standards, manufacturers employ a variety of advanced testing methods that assess the integrity and performance of automotive parts throughout the production process. These methods include dimensional checks using coordinate measuring machines (CMM), surface finish analysis through profilometry, and material strength tests using tensile and compression machines. Non-destructive testing techniques, such as ultrasonic testing, X-ray imaging, and magnetic particle inspection, are also crucial for detecting internal defects without damaging the parts.
Automated systems are also playing an increasingly significant role in maintaining quality throughout the automotive production cycle. Sensors and machine monitors are integral to this process, providing real-time data on machine performance and part quality. This continuous feedback allows for immediate adjustments to be made during the production process, reducing the likelihood of producing defective parts and ensuring consistent adherence to quality standards. Other Internet of Things (IoT) devices, such as smart cameras and laser scanners, are used to monitor the dimensions and surface quality of parts as they are produced. These systems can quickly identify deviations from the standard and alert operators, facilitating a swift response that can correct the error and adjust the machine settings.
Access Reliable and Precise Automotive Tooling at Carr Lane Mfg.
As the automotive industry continues to evolve with increasing demands for precision and efficiency, having the right tooling and components becomes crucial. Selecting the right materials and tooling, employing advanced machining methods, and integrating effective quality control measures can ensure all manufacturing processes achieve the high standards and precision required in the automotive industry.
Carr Lane Mfg. helps automotive manufacturers access the high-quality tooling solutions they need to enhance productivity and quality. Our extensive range of products, from precision jigs and fixtures to robust clamping and positioning systems, is designed to meet the rigorous standards required in the automotive sector. Invest in reliable and high-quality tooling from Carr Lane Mfg. to significantly elevate your production capabilities.
Contact Carr Lane Mfg. today to see how our products can benefit your manufacturing process or to consult with our experts about your specific tooling challenges. We’re here to help you achieve optimal efficiency and precision in your automotive part production and stay competitive in this dynamic industry.
Discuss Your Tooling Needs with Carr Lane Mfg.
Contact Us